Polypipe Building Services recognised for creating a safety culture
Thursday 13th July 2023
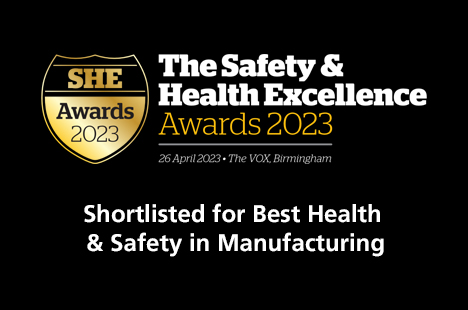
Specialists in providing engineered above ground drainage and water supply systems, manufacturer Polypipe Building Services has been recognised for their work in improving safety at their Kent site at the National Safety & Health Excellence Awards.
Having made it to the national finals in the Best Health & Safety in Manufacturing category they were pipped to the post for the award, but their ongoing work to improve site safety has driven down safety incidents onsite, which flies in the face of the manufacturing sector which continues to feature as one of the highest industries for workplace accidents according to the latest HSE statistics for 2021/22.
Polypipe Building Services Site Health, Safety and Environmental Manager Kevin Rose, said work began over three years ago to generate a mindset shift towards safety from one of compliance to a culture of care. This has led to the appointment of a team of site H & S Advisors, Safety Ambassadors, and a program of safety training which was cascaded from top level management down and has seen a reduction in injuries. We have also seen an increase in near miss reporting and the change of mindset has resulted in improved fork truck behaviours with a significant reduction in fork truck level one impacts being reported.
He said: “Culture isn’t something which is created overnight but by a series of small steps, so putting safety first becomes a natural reaction.
“Historically within manufacturing and construction I think there has been an old school mentality towards safety and reporting of incidents which we need to move away from. Key to changing that is changing the message from the top down that safety comes first, which is why three on-site safety trainers have been appointed at Polypipe – quite a large number for the size of our business.”
More than 200 staff have also gone through Deal With It safety training which continues to be rolled out and aims to give people the confidence to approach someone if they seem them working unsafely.
External training provider Neil Lancaster, of SOG Ltd based in Runcorn said: “We began working with Polypipe Building Services in 2019 to put together a three-hour workshop to complement the company’s own safety procedures and when we came to deliver it the staff totally embraced it.
“The difference with our training is it’s not about making people compliant, it’s about creating a culture of care and empowering people so they feel they can make a difference and take safety seriously.
“The see it, sort it, report it campaign at Polypipe means we look at why most people don’t report everything and ask ‘what are the obstacles to that happening?’
“Reporting means changing people’s attitude from one where it’s seen as ‘grassing someone up’, to realising it’s about looking after yourself and everyone around you because if that person has an accident the person who saw it must live with the consequences.”
As the company works towards a target of zero lost time injuries, 10 safety ambassadors from all levels of the business now act as the eyes and ears of the Kevin’s safety team, conducting weekly safety audits within their department and supporting the Management with the Risk Assessment reviews for the department.
Among them are yard operative Jordan Kerr and assembly operative Elena Ujacov, who both joined the company 12 months ago having never worked in manufacturing before.
Jordan said: “A large part of my role so far has been focussing on improving safety around driving around on site as when you’re driving a forklift around you must be aware of every detail.
“In my department we’ve worked hard to improve driver behaviours and reducing level one impacts, which could be something like driving over a pothole, from an average of 12 level one reports a week to one a week by discussing where the potholes are on site and choosing the safest routes to avoid them.”
Elena said: “It’s been an eye-opener for me as in Moldova the attitude to safety is different as there are no safety shoes, high-vis or hard hats needed.
“I wanted to do it because I care about people and my own safety, and want to work in a safe environment where everyone goes home as they came in.
“When I began working as an ambassador, I started to challenge people if I spotted them doing something unsafe, and I work in a nice team so if I need to ask someone to move something or speak to them about manual handling it’s fine and incidents are low in our area.”
The manufacturing company is currently awaiting the results of its latest HSE ‘Climate’ survey to check that their work towards improving workplace safety is improving the culture within the business, while extensive safety training remains an ongoing process as new staff join the team.
Kevin adds: “We are making a difference and the key thing is to reiterate that everyone has a part to play in this process and if anyone feels they haven’t had sufficient training or feels unsafe, they should ‘Stop the Process’ and any manager in the business will support them.
“Generally, people think they are doing things for the right reasons, they don’t deliberately act in an unsafe way, however everyone can have a different sense of risk perception.
“My target is for there to be zero lost time injuries and to create a safe working environment where people don’t injure themselves to the extent, that they can’t work the next day. That’s a realistic target for me, and that’s the message I communicate across all our teams and our ambassadors.”4